Introduction
Maintaining optimal inventory levels is a critical challenge for any business that holds stock. Order too late and you risk stockouts, lost sales, and dissatisfied customers; order too early and you tie up precious capital in inventory, increasing holding costs and risk of obsolescence. The reorder point (ROP) is a simple yet powerful metric that tells you the exact inventory level at which you should trigger a new purchase order to replenish stock. When calculated correctly—by factoring in average demand, supplier lead time, and safety stock—your ROP ensures you maintain service levels while minimizing excess inventory.
In this comprehensive guide, we’ll dive deep into:
- The core ROP formula
- Detailed steps to calculate each component
- Multiple methods for estimating safety stock
- Adjustments for periodic review systems
- Handling variability in demand and lead time
- Practical tips, real-world examples, and common pitfalls to avoid
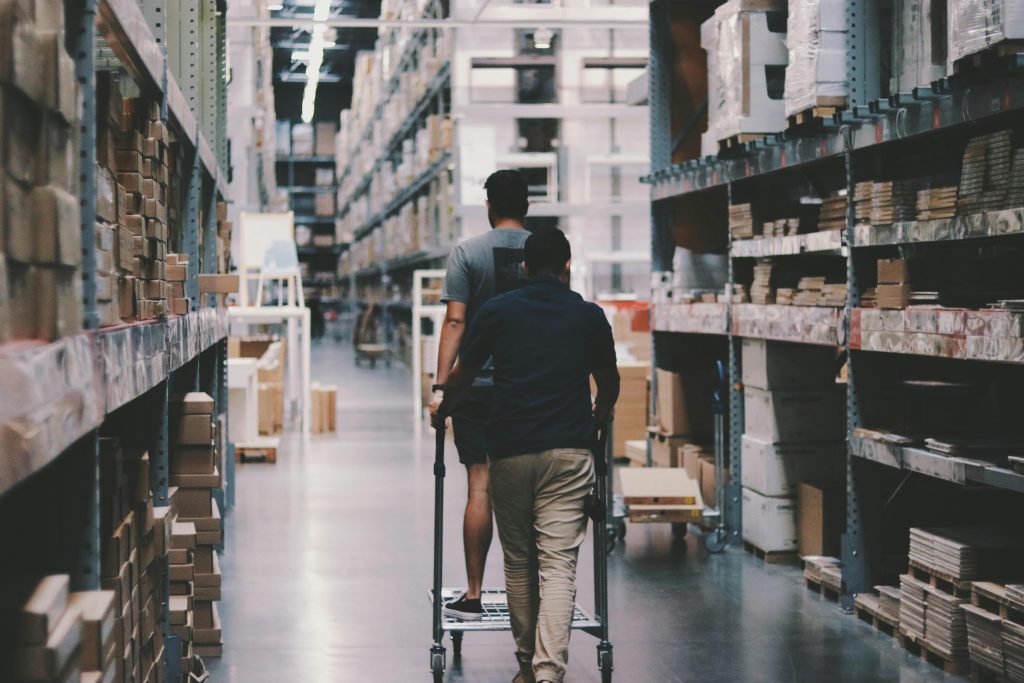
By the end of this post, you’ll have the tools and understanding to implement accurate reorder points across your product lines and keep your supply chain running smoothly.
1. The Core ROP Formula
At its most basic, the reorder point is:
Reorder Point (ROP) = Lead Time Demand + Safety Stock
Where:
- Lead Time Demand = Average Daily Demand × Lead Time (in days)
- Safety Stock = Buffer stock to cover variability in demand and/or lead time
Putting these together gives you a clear trigger: when on-hand inventory drops to the ROP, you place a replenishment order.
2. Calculating Average Daily Demand and Lead Time Demand
2.1 Gather Historical Data
- Time Horizon: Ideally 6–12 months of daily or weekly sales/usage data.
- Data Quality: Exclude one-time promotions, returns, or anomalies that don’t reflect typical demand.
2.2 Compute Average Daily Demand
sqlCopyEditAverage Daily Demand = Total Units Sold over Period ÷ Number of Days in Period
For example:
- If you sold 3,000 units over 90 days, then
Average Daily Demand = 3,000 ÷ 90 = 33.3 units/day
2.3 Determine Lead Time Demand
javaCopyEditLead Time Demand = Average Daily Demand × Lead Time (days)
- If your supplier lead time is 10 days, then
Lead Time Demand = 33.3 × 10 = 333 units
3. Estimating Safety Stock
Safety stock covers unexpected spikes in demand or delays in replenishment. Two primary methods prevail:
3.1 Fixed-Safety Buffer
- Simple to implement: Set the same buffer for all SKUs or per category (e.g., always keep 50 extra units).
- When to use: Low-value items, minimal variability, or when statistical data is insufficient.
3.2 Statistical Safety Stock
Uses standard deviation (σ) and desired service level (z-score) to calculate a data-driven buffer.
- Calculate σ of daily demand over your data period.
- Compute σ of lead time demand: sqlCopyEdit
σLT = σdaily × √Lead Time
- Choose a service level (e.g., 95% in-stock probability → z = 1.65; 99% → z = 2.33).
- Safety Stock = z × σLT
Illustrative example:
- σdaily = 8 units, lead time = 10 days, z = 1.65
- σLT = 8 × √10 ≈ 25.3
- Safety Stock ≈ 1.65 × 25.3 ≈ 42 units
4. Advanced Adjustments
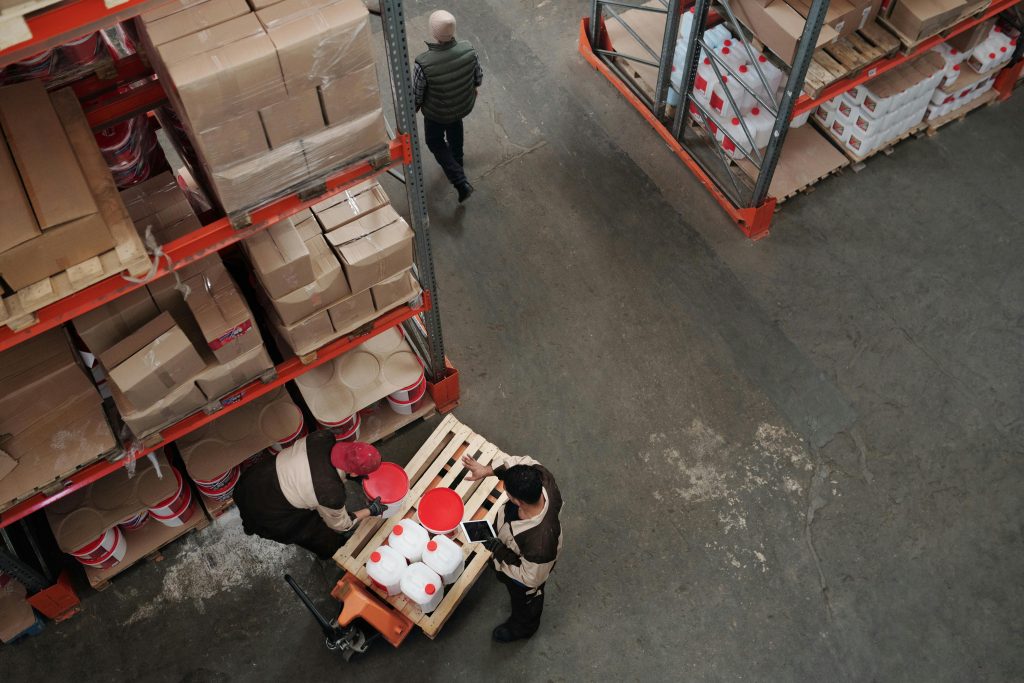
4.1 Periodic Review Systems
If you only reorder at fixed intervals (e.g., weekly or monthly), include the review period:
iniCopyEditROP = Average Daily Demand × (Lead Time + Review Interval) + Safety Stock
For a weekly review (7 days):
- ROP = 33.3 × (10 + 7) + 42 = 33.3 × 17 + 42 = 566 + 42 = 608 units
4.2 Variable Lead Time
When lead times fluctuate, incorporate lead time variability into σLT:
sqlCopyEditσLT = √[(Average Demand² × σLT_days²) + (σdaily² × Lead Time²)]
- σLT_days = standard deviation of lead time in days
- σdaily = standard deviation of daily demand
This combined approach ensures your safety stock covers both demand and supply uncertainties.
5. Real-World Example
Input | Value |
---|---|
Average Daily Demand | 33.3 units/day |
Lead Time | 10 days |
σdaily | 8 units |
Desired Service Level | 95% (z = 1.65) |
Review Interval (if periodic) | 7 days |
Step 1: Lead Time Demand
Lead Time Demand = 33.3 × 10 = 333 units
Step 2: σLT
σLT = 8 × √10 ≈ 25.3
Step 3: Safety Stock
Safety Stock = 1.65 × 25.3 ≈ 42 units
Step 4: ROP (Continuous Review)
ROP = 333 + 42 = 375 units
Step 5: ROP (Weekly Review)
ROP = 33.3 × (10 + 7) + 42 = 608 units
6. Practical Tips for Accurate ROPs
7. Common Pitfalls to Avoid
- Ignoring Lead Time Variability: Using a fixed lead time when suppliers frequently miss delivery windows will lead to stockouts.
- Over-Buffering C-Items: Applying the same statistical safety stock to slow-moving, low-value items ties up capital unnecessarily.
- Neglecting Data Quality: Outliers (promotional spikes, returns) can skew averages and standard deviations—clean your data first.
- Static ROPs in Dynamic Markets: Failing to update ROPs in response to sales growth or seasonality leads to obsolete triggers.
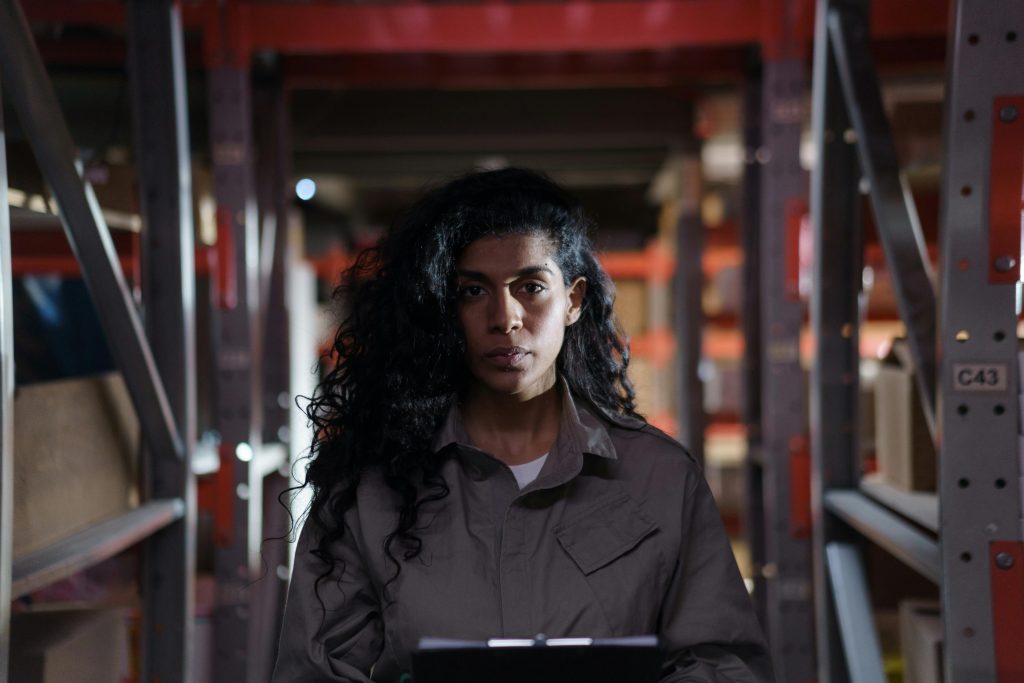
Conclusion
A well-calculated reorder point is the cornerstone of efficient inventory management. By systematically combining average demand, lead time demand, and safety stock—whether via a simple fixed buffer or a robust statistical model—you’ll ensure timely replenishment while minimizing excess stock. Remember to adjust for periodic review intervals, account for variability in both demand and supply lead time, and segment your SKUs based on movement and value. Regularly revisit and refine your calculations to keep pace with changing business conditions. Implement these best practices, and you’ll maintain high service levels, optimize working capital, and build a more resilient supply chain.